Why Predictive Maintenance in Manufacturing Requires Strong Cybersecurity
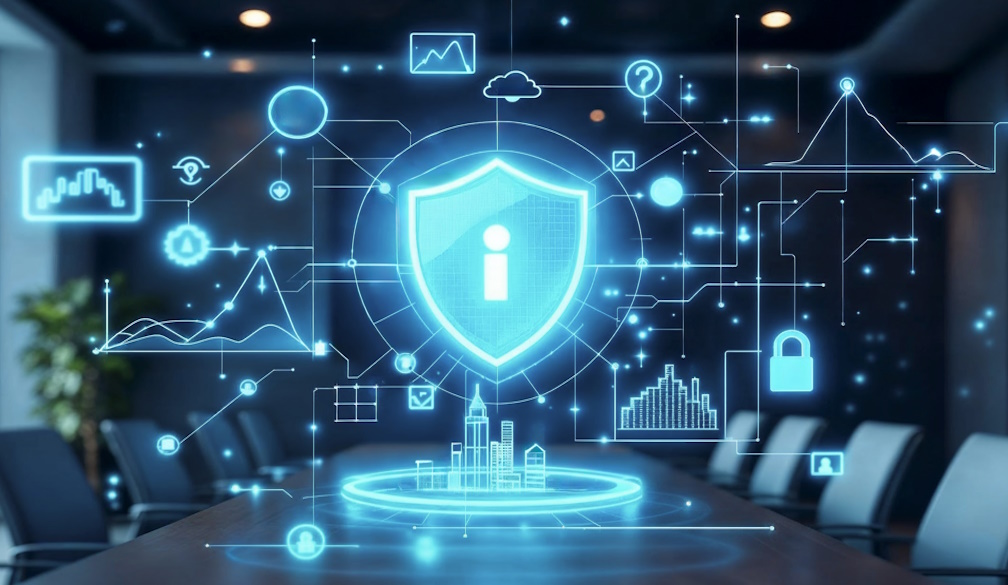
Predictive maintenance has become a cornerstone of modern manufacturing. By using sensors and real-time data to detect wear and tear before machines fail, manufacturers can reduce downtime, save money, and increase productivity. But while the focus is often on keeping machines running smoothly, there’s a critical side of predictive maintenance that often gets overlooked: cybersecurity. These systems rely heavily on network-connected devices and cloud analytics, making them vulnerable to attacks. If compromised, the very data used to prevent breakdowns could become a source of disruption. That’s why protecting predictive maintenance systems is no longer optional. It’s essential.
The Power and Risk of Predictive Maintenance
Predictive maintenance systems work by collecting performance data from machines using IoT sensors and feeding that data into analytics platforms that spot patterns and detect potential failures. This technology saves companies millions by allowing maintenance teams to act before costly breakdowns occur. But the very fact that these systems are connected, often to both internal networks and third-party analytics providers, opens the door to cyber threats. If hackers manipulate sensor data or block communication, it can lead to false alarms, missed warnings, or even deliberate equipment failures. What helps avoid downtime could ironically create it.
Securing the Data That Powers Maintenance Decisions
The value of predictive maintenance depends on the accuracy and integrity of the data it uses. If that data is altered, delayed, or stolen, maintenance schedules could become unreliable and unsafe. This is especially concerning in sectors like food processing or pharmaceuticals, where equipment performance directly impacts product safety. Securing these systems requires more than just firewalls. It means implementing role-based access controls, encrypting data in transit, and isolating sensitive operational networks. Manufacturers must treat predictive maintenance data with the same caution they use for financial or intellectual property data. It’s just as valuable.
Choosing the Right Detection and Response Approach
As predictive maintenance becomes more common, manufacturers are rethinking how they monitor and protect their digital systems. Choosing between EDR vs MDR vs XDR often depends on the complexity of the network and the level of in-house expertise. EDR focuses on protecting specific endpoint devices like control stations. MDR brings in outside experts to handle detection and response across a broader set of tools. XDR provides a unified view by pulling data from multiple sources, including IoT devices and cloud platforms, allowing for faster, context-rich responses. Each approach offers different strengths depending on how predictive maintenance systems are deployed.
Don’t Overlook the Human Element
Even the best cybersecurity tools can’t fix careless behavior. Many breaches in manufacturing environments start with simple human mistakes, like connecting a personal device to a maintenance dashboard or falling for a phishing email disguised as a vendor alert. That’s why regular training is just as important as strong technical safeguards. Maintenance staff and IT teams must understand the specific threats that could impact operational technology. Simple rules, like never using shared logins or always updating passwords, can go a long way. A well-informed team can act as the first and strongest line of defense against threats.
Making Security Part of the Maintenance Culture
Predictive maintenance isn’t just about tech. It’s a mindset shift toward prevention. That same mindset needs to extend to security. Instead of reacting to cyber threats after they happen, manufacturers must adopt proactive protection strategies that evolve with their operations. As machines get smarter, so do attackers. By making cybersecurity part of the maintenance conversation, companies protect not just their machines, but their data, productivity, and reputation. In a connected factory, maintenance and security go hand in hand. You can’t afford to optimize one while ignoring the other.