Understanding the different types of coveralls and their importance
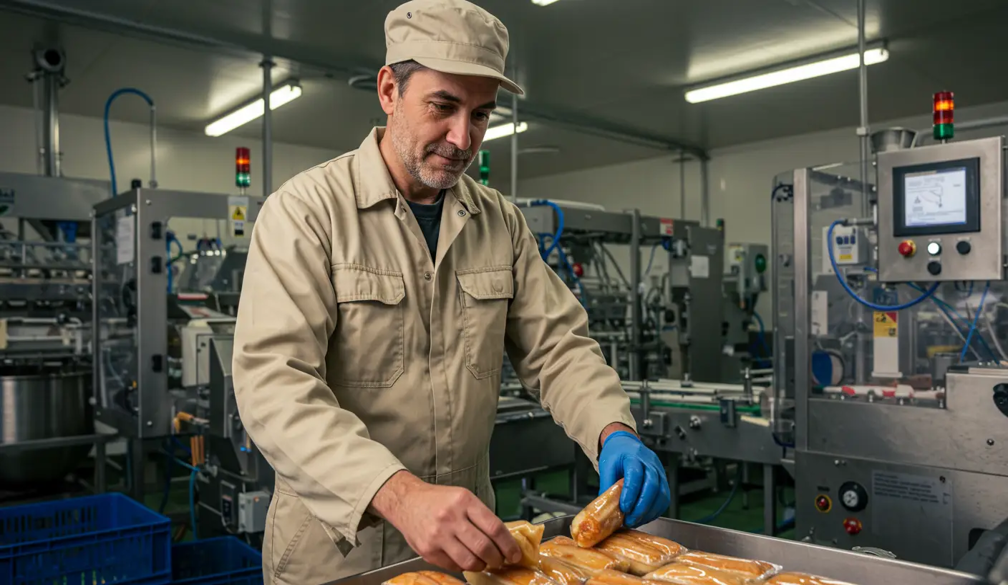
Coveralls provide complete coverage to protect employees from a range of workplace dangers; it is a crucial piece of personal protective equipment (PPE). By covering the body, including the arms and legs, coveralls act as a barrier against physical, chemical, biological, and environmental risks. Their use in a variety of sectors, such as manufacturing, healthcare, oil and gas, and construction, highlights their significance and adaptability.
Types of Coveralls
It is essential to choose the right type of coveralls to ensure workers' safety and compliance with industry standards. Below are some common categories:
1. Standard Work Coveralls
These coveralls are usually composed of sturdy materials like blends of cotton and polyester, which can be used daily. They protect against dirt, grease, and minor abrasions to make them ideal for factory workers, mechanics, and landscapers.
2. Flame-Resistant (FR) Coveralls
FR coveralls are made of materials that resist ignition and prevent flames from spreading, such as Nomex or treated cotton. They are crucial to wear in fire-hazardous industries like welding, oil and gas, and firefighting. They protect from the risk of burns and enhance worker safety in high-temperature environments.
3. High Visibility Coveralls
High visibility coveralls are essential for people working in dimly lit areas or near moving vehicles. They ensure that workers remain visible because of their fluorescent colors and reflective strips to prevent them from accidents. These coveralls adhere to standards such as the American National Standards Institute (ANSI) classifications for high visibility apparel.
4. Insulated Coveralls
Insulated coveralls provide thermal protection to keep the body warm, specifically designed for cold weather. They are right for working outdoors during the winter or in temperature-controlled warehouses to ensure comfort and avoid cold-related illnesses.
5. Waterproof Coveralls
Wearing waterproof coveralls made of coated nylon or PVC keeps workers dry in damp conditions. They prevent water penetration and maintain comfort during prolonged exposure to moisture and are commonly used in agriculture, fishing, and outdoor construction.
6. Disposable Coveralls
Disposable coveralls are an affordable option for jobs requiring frequent clothing changes or involving non-hazardous contaminants. Made of lightweight materials, they are frequently used for painting, cleaning, and hygienic purposes in medical settings.
Importance of Coveralls
The utilization of coveralls in the workplace serves multiple critical functions:
1. Protection from Physical Hazards
Coveralls offer an extra line of protection against sharp objects, machinery, and debris in settings like construction sites where workers run the risk of getting cuts, abrasions, or impacts.
2. Shielding Against Chemical Exposure
Coveralls prevent skin contact and absorption by acting as a barrier against hazardous chemicals. In sectors where exposure to hazardous materials is common, such as manufacturing and laboratories, this protection is essential.
3. Fire and Heat Resistance
Flame resistant coveralls are indispensable in occupations with fire risks. By deterring ignition and stopping the spread of flames, they reduce burn injuries and improve worker safety in hot environments.
4. Enhanced Visibility
High visibility coveralls make sure that workers are visible in low light or busy areas, which lowers the chance of accidents involving cars or machinery. It ensures appropriate visibility levels by following standards like ANSI/ISEA 107.
5. Environmental Protection
Waterproof and insulated coveralls shield employees from the elements in inclement weather, such as rain or cold, preserving their comfort and averting weather-related illnesses.
6. Hygiene and Contamination Control
Coveralls prevent the spread of contaminants to ensure a sterile environment and safeguard both workers and products in sectors like healthcare and food processing.
How to Choose the Right Coveralls
Selecting suitable coveralls involves evaluating several factors:
1. Assess Workplace Hazards
Determine the required protective features by identifying potential risks, such as exposure to chemicals, flames, or poor visibility.
2. Material Selection
Choose materials that provide the right protection and comfort. For example, polypropylene offers chemical resistance, while Nomex offers flame resistance.
3. Proper Fit and Comfort
To allow for mobility without being too loose or restrictive, make sure that coveralls fit well. Comfort is crucial for both effectiveness and extended wear.
4. Compliance with Safety Standards
Ensure that the coveralls meet relevant safety standards, such as those set by ANSI for high visibility apparel.
5. Additional Features
Depending on the demands of the job, features like ventilation, reinforced knees, or pockets can improve comfort and functionality.