Work Order Management Software for Manufacturing: Key Features and Use Cases
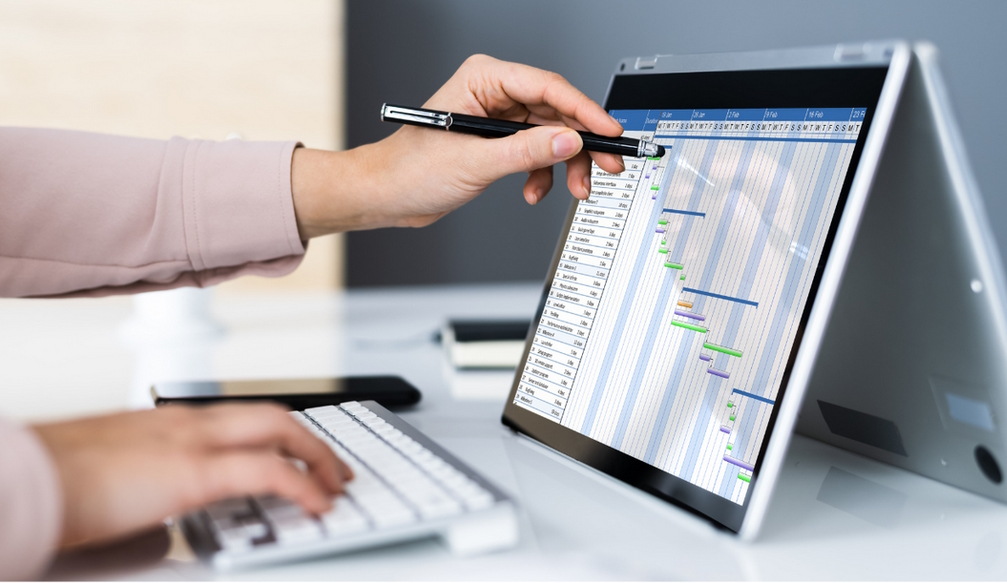
Efficient work order management is crucial for the success of any manufacturing business. Manufacturing operations require streamlined processes to ensure that all activities are carried out smoothly, and the final product meets the required standards. This is where work order management software comes in, providing manufacturers with a tool to help plan, schedule, and track their production processes.
In this blog, we will explore the key features of work order management software for manufacturing and its use cases.
Key Features of Work Order Management Software
Work order management software has the following key features:
1. Centralized Work Order System
Work order management software provides a centralized system for all work orders, including equipment maintenance, inventory management, and production scheduling. This system allows manufacturers to create, assign, and track work orders, providing complete visibility of the production process.
2. Real-time Updates
Work order management software provides real-time updates on the status of work orders, allowing manufacturers to quickly identify and address any issues that may arise. This feature ensures that production runs smoothly and helps to minimize downtime.
3. Inventory Management
Work order management software helps manufacturers manage their inventory levels by providing real-time updates on stock levels and automatically generating purchase orders when stock levels run low. This feature ensures that manufacturers always have the necessary inventory on hand to meet production demands.
4. Preventive Maintenance
Work order management software can also help manufacturers to schedule and track preventive maintenance tasks. By scheduling regular maintenance tasks, manufacturers can minimize downtime and ensure that their equipment remains in optimal working condition.
5. Reporting and Analytics
Work order management software provides manufacturers with detailed reporting and analytics, enabling them to identify areas for improvement and make informed decisions. This feature allows manufacturers to track key metrics, such as downtime, productivity, and maintenance costs.
Use Cases of Work Order Management Software
Work order management software has the following use cases:
1. Production Planning and Scheduling
Work order management software can help manufacturers to plan and schedule their production processes. By creating work orders and scheduling tasks, manufacturers can ensure that their production processes run smoothly and efficiently.
2. Equipment Maintenance
Work order management software can also help manufacturers to schedule and track equipment maintenance tasks. This feature ensures that equipment is properly maintained and reduces the risk of breakdowns or failures.
3. Inventory Management
Work order management software can help manufacturers to manage their inventory levels and ensure that they always have the necessary materials on hand to meet production demands.
4. Quality Control
Work order management software can also help manufacturers to implement and maintain quality control processes. By creating work orders and tracking production processes, manufacturers can ensure that their products meet the required quality standards.