The Advantages of Lean and Six Sigma
- Written by Ester Adams
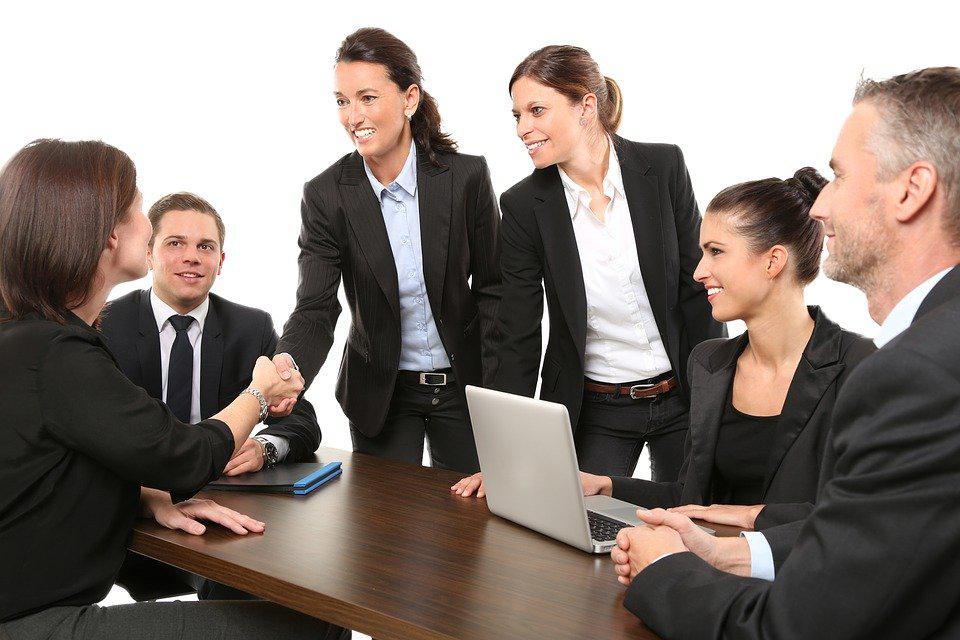
When running a business, there should be less or no room for error at all. Although it’s inevitable for some businesses to suffer loss, there are still methods to prevent a huge loss. These methods ensure that the company fully utilizes every tool and workforce they have within their grasp.
For companies to gain some traction, there is a lean six Sigma training that they can attend to know which aspects of the company they need to improve. Other companies might brush aside this training and think of it as a waste of time, which leads to a road filled with potholes of unresolvable problems.
A Brief Definition of the Method
Six Sigma centres on lessening process variation and strengthening process control, while Lean eliminates unnecessary processes and encourages workflow and standardization. You can say that the divergence between the two is blurry, so they were fused, and people created the term “Lean Six Sigma.” Trainers use this term frequently because process improvement needs the aspects of both to achieve pragmatic results.
Lean Six Sigma is a philosophy driven by data and facts, and it all pertains to preventing defects rather than detecting defects. Prevention is always better because companies have more time to resolve the issue compared to when the problem is already too late to resolve. Once a company utilizes the lean six Sigma, they experience all sorts of benefits that will help them grow exponentially.
Increased Profits
Organizing a company’s profit is what lean six Sigma can do. Sometimes, companies would spend extra, unnecessary resources to gain more profit. The lean six Sigma training helps the company eliminate this problem and opens opportunities to utilize fewer resources while gaining profit.
Decreased Costs
When talking about removing waste in a company, this means to get rid of useless activities that take up more time than productivity. A good example is the reduction of the steps and processes of creating a product. Once a company figures out which steps are no longer needed, production time is significantly cut down, and valuable time and resources are saved. It can also help determine where hiccups mostly happen within the company and prevent them from turning into a bigger problem.
Improved Efficiency
Whether it’s a worker or a manager, there are ways to do their job even better. In some cases, the old method they’ve been doing for years might not fit today’s age. The old methods might even drain a company’s valuable resources, so teaching them new and efficient methods is the best option.
Lean Six Sigma helps companies provide standard processes that are not difficult to learn, enhance, and operate. When the processes are implemented, they can free up valuable resources and allocate them somewhere else to benefit the company even more.
Create a Unified Team
The workforce is the lifeline of any company. Ensuring they work as a cohesive unit is critical in keeping the company afloat. The lean six sigma training would usually start with the leader and then passed on to succeeding members. This ensures each leader can handle the workload, build trust with everyone, and get the job done right.
You need to be wise when running a company. Even when a company is earning so much, there’s always more room for improvement. With lean six Sigma training, efficient workers are created, and more growth opportunities are opened.
Author Bio: Ester Adams is a farmer of words in the field of creativity. She is an experienced independent content writer with a demonstrated history of working in the writing and editing industry. She is a multi-niche content chef who loves cooking new things.